Categories: How does it work
Number of views: 23713
Comments on the article: 1
How the plasma welding machine is arranged and works
Plasma in physics is the fourth state of matter after solid, liquid, and gaseous forms, when partial or complete ionization of the medium from previously neutral molecules and atoms occurs under the condition of quasineutrality: the volume density of all charged particles is equal.
In welding technology, the following properties of low-temperature (less than a million degrees Kelvin scale) plasma are used:
-
very high electrical conductivity;
-
the strong influence of external magnetic fields on the flow of currents in it, contributing to the formation of jets and layers;
-
manifestation of collective effects, expressed by the predominance of magnetic and electric forces over gravitational.
Principles for creating and operating plasma torches
In this welding method, the source of heating metals to the melting point is a plasma arc of ionized gas, which is directed in the right direction. It is produced by a special device called a plasmatron or plasma torch.
Classification by type of arc
By the principle of operation, the plasmatron can be of direct or indirect action.
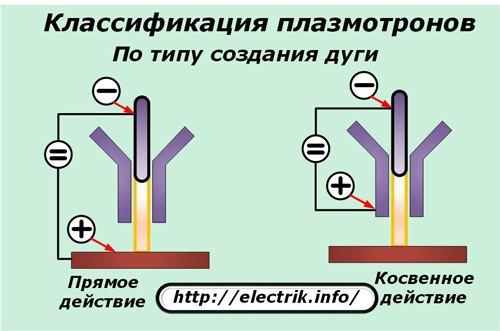
In the first case, the potential difference of the external field of the generator, creating the conditions for the formation of an arc, is applied directly to the workpiece and the electrode of the gas burner. Due to this, the cooling efficiency of the structure is increased.
In the second method, electrical voltage is applied only between the parts of the burner to create a plasma jet. Due to this, it is necessary to complicate the cooling system of the nozzle assembly.
For direct-acting plasmatrons, an arc is produced that approximately resembles a cylindrical shape, expanding slightly at the surface of the metal being processed.
Inside the neutral electric nozzle, compression and stabilization of the arc occurs. In this case, the combination of the thermal and kinetic energy of the plasma forms an increased power for it, which allows the metal to melt deeper.
Indirect burners create a plasma in the form of a conical jet surrounded by a torch directed toward the product. The jet is blown out by the plasma stream coming from the burner.
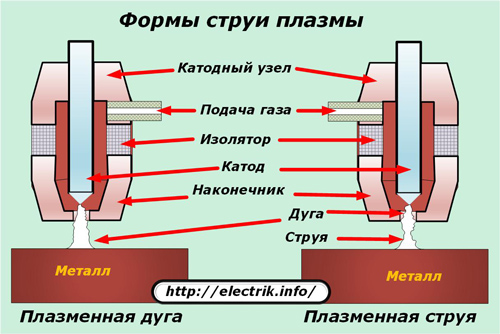
Classification of burner cooling methods
Due to the high temperature of the plasma, various methods of cooling the details of the plasma torch are used:
-
blowing air;
-
heat removal due to forced circulation of water.
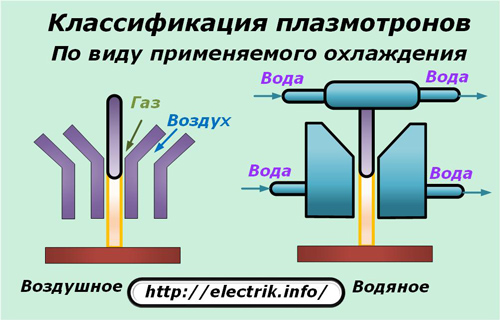
Air cooling is less expensive, and liquid cooling is the most efficient, but complex.
Classification of arc stabilization methods
The gas burner should provide an even, stable in size and direction temperature column with strict fixation of it along the axis of the nozzle and electrode.
To this end, three types of nozzle designs using energy have been developed:
1. gas;
2. water;
3. magnetic field.
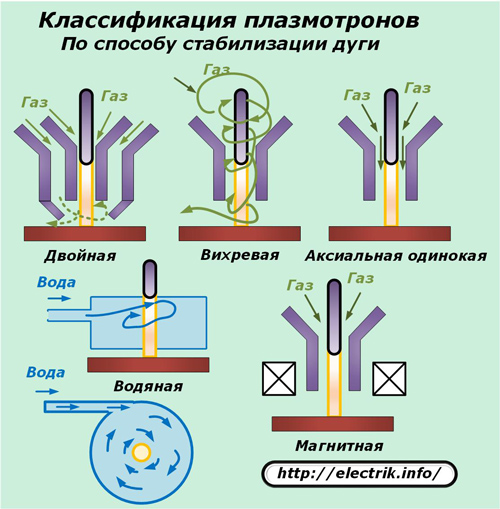
In the first method a cold stream of gas, blowing a column of plasma, cools and simultaneously compresses it. Depending on the direction of the gas stream, stabilization is created:
1. axial - with parallel blowing of the column;
2. swirling when the gas flow is created in the perpendicular direction.
The second method compresses the arc more efficiently and is used in plasmatrons used for metal deposition or cutting.
Axial stabilization is better suited for welding and surfacing of metals.
The double stabilization scheme combines the features of axial and vortex. When using it, it is possible to pass gas in three ways:
-
only through the main central channel;
-
through both;
-
exclusively through external.
Each method creates different schemes for compressing the plasma column.
Water stabilization uses counter swirling fluid flows.The steam generated in this process helps to create plasma with a column heating up to 50 thousand degrees on the Kelvin scale.
A significant drawback of this method is the intense combustion of the cathode. For such devices, the electrode is made of graphite, developing mechanisms for its automatic approach to the workpiece as the length is continuously consumed.
Water-stabilized plasma torch devices are noted:
-
design complexity;
-
low reliability of the electrode feed system;
-
the complexity of the methods of excitation of the arc.
Magnetic stabilization It works due to the directional magnetic field located across the movement of the arc column. Its efficiency is the lowest, and the solenoid built into the nozzle greatly complicates the plasma torch circuit.
However, magnetic stabilization is used to impart rotational motion to the anode spot within the walls of the nozzle. This allows to reduce the erosion of the nozzle material, which affects the purity of the plasma jet.
All the constructions of plasmatrons considered above are arc ones. But there is another type of similar plasma generating devices due to the energy of the high-frequency current passing through the inductor coil. Such plasmatrons are called induction (HF) and they do not require electrodes to create an arc discharge.
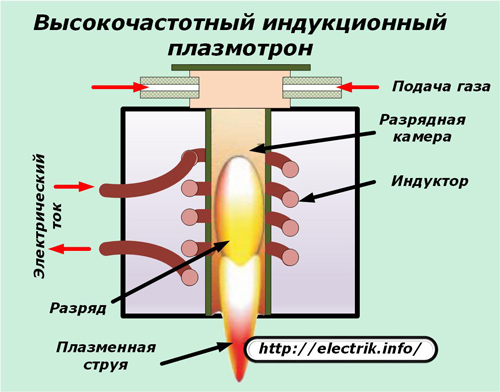
They do not have special advantages in influencing the processed metals in comparison with arc devices and are used to solve individual technological processes, for example, the production of pure powder metals.
Design features of burners
The operation of one of the types of plasma torches can be explained by the figure below.
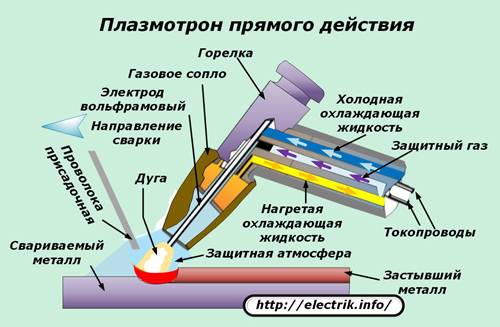
The plasma arc during welding is created inside the protective atmospheric shell formed by supplying injected gas to the working area. They most often choose argon.
Plasma-forming gas (ionization source) can work:
-
argon;
-
nitrogen;
-
helium;
-
air;
-
hydrogen;
-
mixtures of the listed gases.
Keep in mind the features of their operation:
-
hydrogen is explosive;
-
nitrides and ozone are released from the air;
-
helium dear;
-
Nitrogen at high temperatures affects the environment.
Tungsten is most often chosen as the material for the electrodes because of the most suitable mechanical properties and resistance to high temperatures.
The gas nozzle is fixed in the burner and is blown with a protective stream. Cold fluid is pumped along the hydraulic lines and heated is discharged.
Current-carrying wires supply electric energy of direct or alternating current to the electrodes.
To power the plasma-forming arc, a current source with a voltage of about 120 volts is connected for welding and about 300 at idle - for cutting.
Plasma Generator Device
Alternating current or direct current can be used to start the plasmatron. As an example, consider the operation of a generator from conventional power supply network 220 volts.
Ballast resistor limits supply current. The throttle controls the load. The diode bridge converts an alternating voltage to maintain a duty arc.
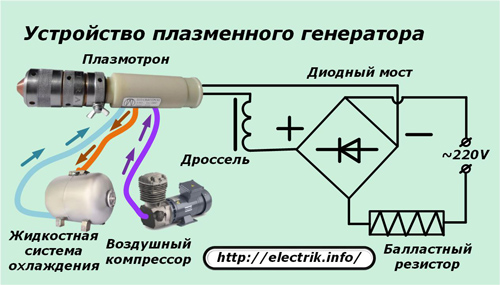
An air compressor delivers shielding gas to the burner, and a hydraulic cooling system circulates the fluid in the plasma lines to maintain effective heat removal.
Technique for plasma welding and cutting
To ignite and maintain the welding arc, electric current energy is used, and for its non-contact excitation, an oscillator (oscillation source).
The use of a pilot arc between the electrode and the nozzle can significantly facilitate the process of starting the plasma.
Such welding will allow joining almost all metals and alloys located in the lower or vertical plane.
Without preprocessing the edges, bevels with a thickness of up to 15 mm can be welded to bevels.In this case, a characteristic penetration with specific forms is formed due to the exit of the plasma jet beyond the back of the welded part through the through slots.
In fact, plasma welding in most cases is a double continuous process:
-
cutting through the workpiece material;
-
welding site cut.
Cutting technology is based on:
-
molten metal layer at the treatment site;
-
blowing the liquid fraction into the plasma stream.
The thickness of the metal affects the cutting technology. For thin products, the indirect method arc is used, and for thicker ones, direct-connected plasma torches work better.
Plasma cutting is the most economical for all metals, including carbon steel.
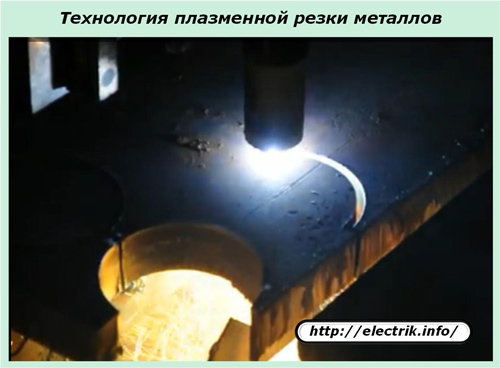
To perform plasma welding and cutting, automated lines and manual installations have been developed.
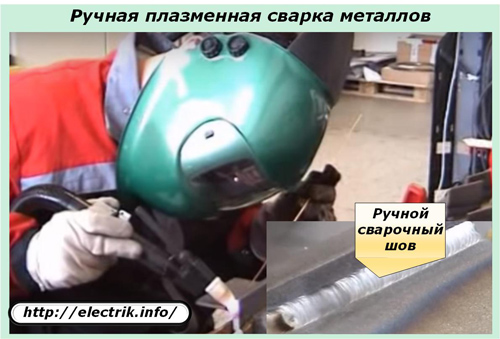
Types of plasma welding
The power of the applied current affects the power of the created arc. Three types of welding are determined by its size:
1. microplasma;
2. average;
3. at high currents.
Microplasma welding
It operates on currents limited to 0.1 ÷ 25 amperes. This technology is used in electronics, instrumentation, jewelry, manufacturing bellows, membranes, thermocouple, foil, thin-walled pipes and containers, allowing you to firmly connect parts with a thickness of 0.2 ÷ 5 mm.
To process different materials, combinations of plasma-forming and protective gases, the degree of compression of the arc, and proximity to the anode are selected. When processing especially thin materials, the pulse mode is used for low-ampere arc supply with the supply of bipolar current pulses.
During the passage of a pulse of one polarity, metal is deposited or welded, and when paused due to a change in direction, the metal cools and crystallizes, and a weld point is created. For its good education, the process of supplying current and pause is optimized. In combination with amplitude control and electrode removal, this allows to achieve high quality compounds of various metals and alloys.
To perform microplasma welding, many technologies have been developed that take into account different angles of inclination of the plasma torches, creating transverse vibrations for the destruction of oxide layers, moving the nozzle relative to the weld being processed, and other methods.
Plasma welding at medium currents of 50 ÷ 150 amperes used in industrial production, mechanical engineering and repair purposes.
High currents from 150 amperes are used for plasma weldings that process industrial alloyed and low-carbon steels, alloys of copper, titanium, aluminum. It allows you to reduce the cost of cutting edges, to increase the productivity of the process, to optimize the quality of the seams in comparison with electric arc methods of joints.
Plasma metal surfacing and surface spraying
Individual machine parts require the provision of high-strength or resistant to high temperatures or aggressive environments surfaces. To this end, they are coated with a protective layer of expensive metal by plasma treatment methods. To do this, the prepared wire or powder in fine granules is introduced into the plasma stream and sprayed in the molten state onto the surface to be treated.
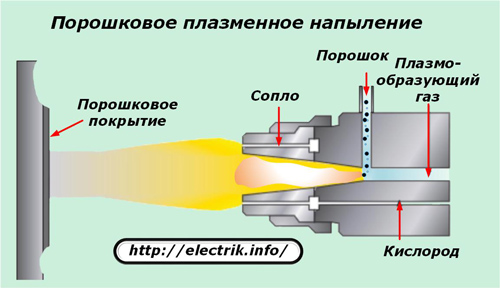
Advantages of this method:
-
the ability of plasma to melt any metals;
-
the ability to obtain alloys of different compositions and create multilayer coatings;
-
the availability of processing forms of any size;
-
convenience of adjusting the energy characteristics of processes.
Advantages of Plasma Welding
The arc source created by plasma welding differs from ordinary electric:
1. a smaller contact area on the treated metal;
2. greater thermal effect due to the approach to a cylindrical shape;
3. increased mechanical pressure of the jet on the metal (about 6 ÷ 10 times);
4. The ability to maintain arc burning at low currents, up to 0.2 amperes.
For these four reasons, plasma welding is considered more promising and multi-purpose in metal processing. It provides better melting within a reduced volume.
The plasma arc has the highest temperature concentration and allows you to cut and weld metals of increased thickness even with certain increases in the distance from the burner nozzle to the workpiece.
In addition, plasma welding devices differ:
-
relatively small dimensions;
-
reliability in work;
-
simplicity of power regulation;
-
easy start;
-
fast termination of the operating mode.
disadvantages
The high cost of equipment limits the widespread introduction of plasma welding in all industries and among small enterprises.
See also at e.imadeself.com
: